Diesel & Gasoline Blending Monitoring
During the blending process, different fractions of the crude oil distillation are mixed together to produce ready-to-sell diesel or gasoline. This process is the most economical when it is carried out in automated process systems that work online. The endpoint of the blending process is reached when the required fuel specifications are achieved. Key characteristics, which indicate the progress of the blending process, are the cetane number for diesel blends and the octane rating for gasoline blends.
Near-infrared spectroscopy (NIR) sensors located directly in the process enable the entire process to be controlled and ensure a high-quality end product.
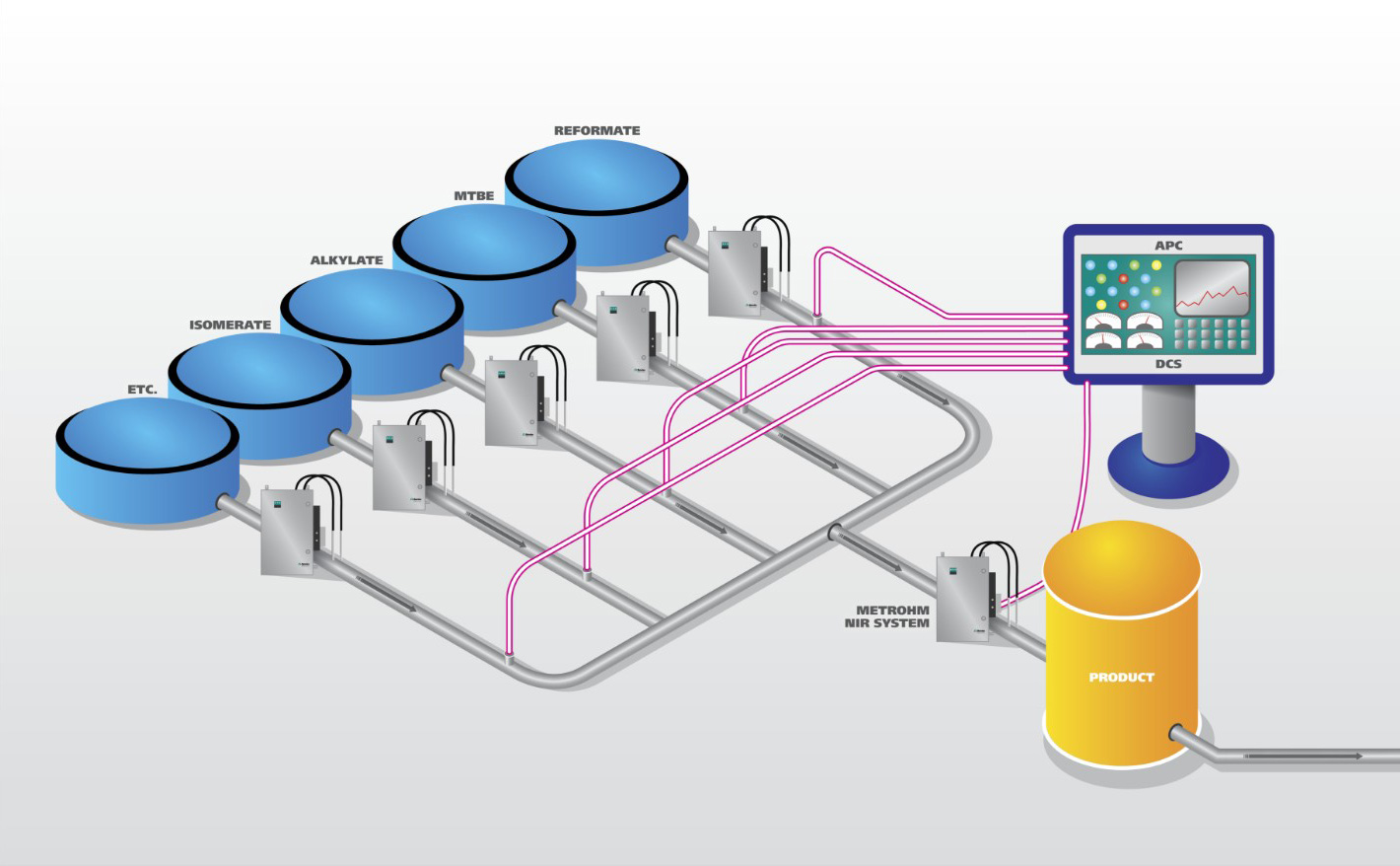
Advantages of NIR Analysis in Petrochemistry
Near-infrared spectroscopy has been successfully used in oil refineries for years. NIR detects numerous parameters in a single measurement in less than a minute. The cost savings are enormous. Further advantages are:
- Short response times and fast quality control
- Improved product quality and process optimization
- Reduced investment, analysis, and maintenance costs
- Accurate and precise measuring results.
Real Time Blending Process Monitoring by NIR
Monitoring the blending of a range of fuels is a direct example of the success of NIR in the refinery. NIR detects numerous parameters in a single measurement in less than a minute. Metrohm manufactures dedicated lab and process NIR analyzers for diesel and gasoline analysis and blend monitoring. These dedicated analyzers are provided with start-up calibration that eliminates time-consuming calibration development.