Ethylene Cracking
Approaching 150 million tons per year, ethylene is the largest volume industrially produced organic material. Feedstock, typically naphtha or light gases (e.g., ethane, propane), is first heated to high temperatures to break down the feed into small hydrocarbon molecules. After being cooled, the products are then sent through a variety of separation processes with high purity ethylene being one product stream among many.
Process optimization focuses on maximizing the output of ethylene and other profitable products. Typically, a Process GC is utilized for monitoring the cracking process. However, these measurements are time-consuming and maintenance-heavy. Near-IR with multicomponent analysis capability can be used for real-time cracking process monitoring.
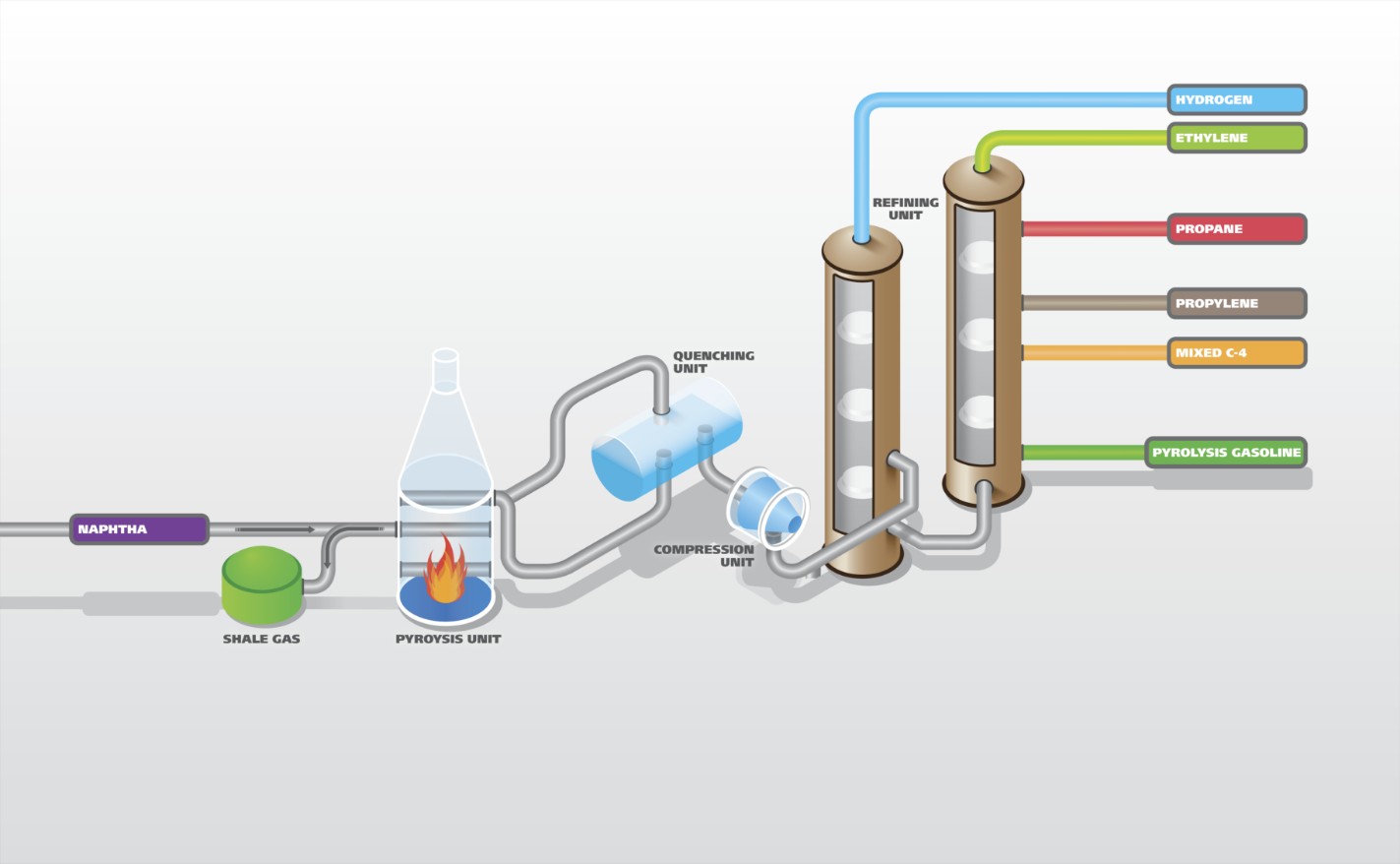
NIR process analysis is a key component of process optimization because it provides process control with real-time gas concentrations at various points in the process. The use of fiber optics enables real-time sequential measurements of up to 9 positions (e.g., feed, recycle streams, product streams) with a single instrument. This allows for rapid adjustments of the process to account for changes such as differences in feed or temperature. The net results of incorporating NIR into the process are increased capacity, improved process reproducibility and product quality. Further, the amount of process testing can be shortened while enhancing plant safety. In combination with a high pressure cell, NIR spectroscopy can also be used as a tool for online, real-time analysis of industrial gases.