Process Improvement & Protection
Increase your profit through internal process improvement
Petroleum refineries are large and complex production facilities. Once the crude oil price is fixed the profitability can only be improved through the process optimization. In plant operation, plant integrity and safety, production rate, product quality, and costs are primary considerations. These all depend on comprehensive process control through online and near-real-time monitoring of key process variables, often in explosive, dusty, corrosive, and hostile environments. Metrohm provides on-line analyzers specifically tailored to your process needs. In addition to the dedicated analyzers, we specialize in suitable sample preconditioning systems that allow you to implement a reliable online solution.
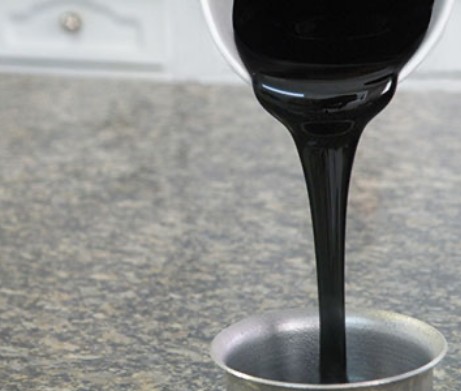
Crude Desalting
Excessive amounts of chloride salts in crude oil result in higher corrosion rates in refining units and have a detrimental effect on the catalysts used. Desalting techniques are well established, but continuous monitoring of the salt content is needed for process control and cost reduction. Salt in crude oil is determined by titration as per ASTM D6470 or by Conductometric measurement as per ASTM D3230.
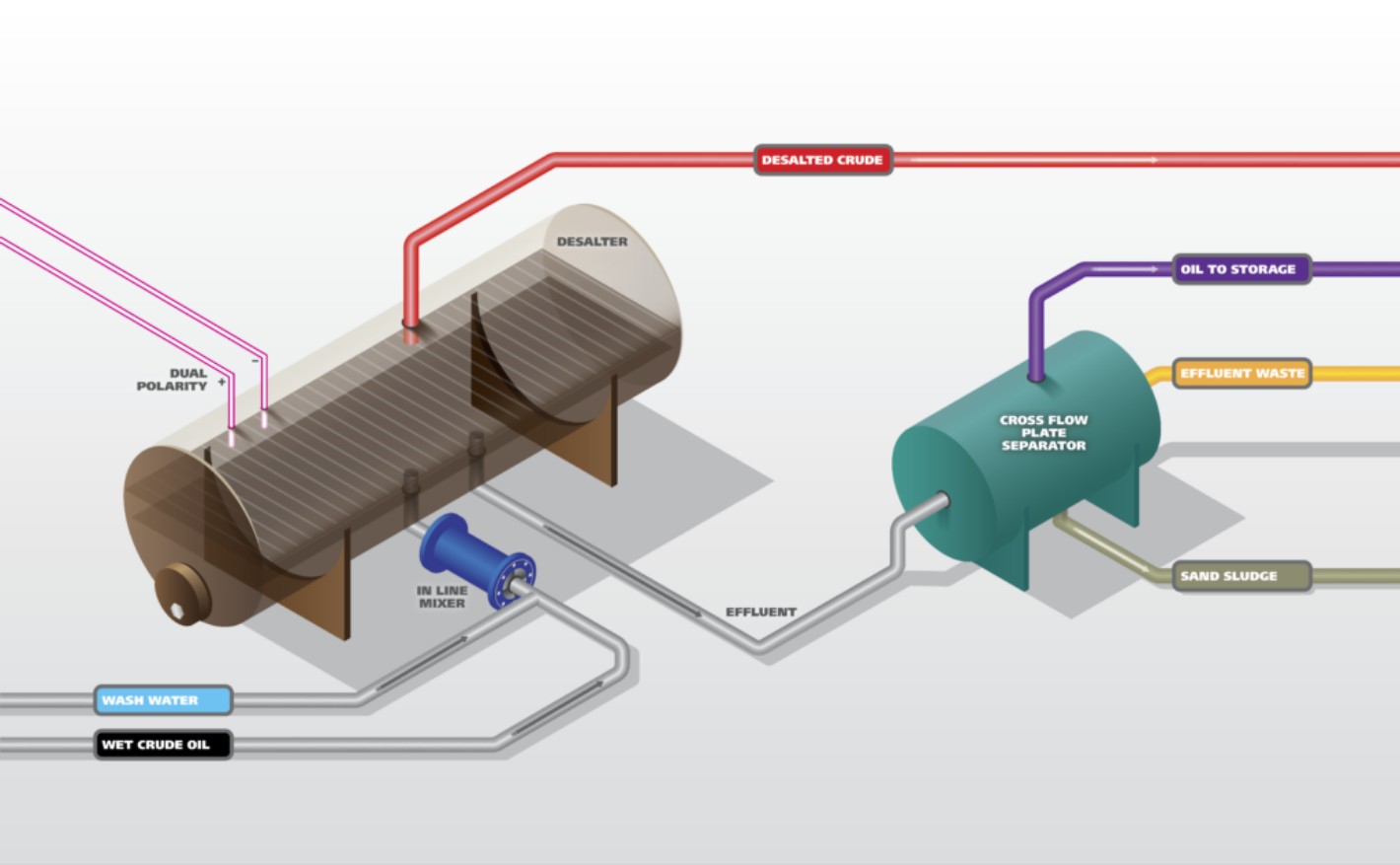
Isobutane and olefin are feeds into the alkylation unit which combines the olefin with butane to increase octane and lower the vapor pressure of the product for blending. Alkylation is used in combination with fractional distillation, catalytic cracking and isomerization to increase the yield of automotive gasoline. Either sulfuric or hydrofluoric acid is used as the catalyst for the alkylation reaction. Both catalysts operate at low temperatures and high isobutane-to-olefin ratios to reduce the side reactions and catalyst consumption. Sulfuric acid is a liquid under normal operation conditions, while hydrofluoric acid is a gas. Produced alkylates are passed through caustic to remove residual acids.
Sour water is condensed wastewater produced during many downstream refining processes containing hydrogen sulfide, ammonia and other contaminating compounds. It is often acidic in nature and can cause corrosion problems within the refineries pipework so it must be treated before it can be reused or disposed to the waste treatment plant.
An amine treating unit captures hydrogen sulfide and other acidic gases from the refinery gas streams and concentrates them into an amine solution. It is also used to capture acidic gases from “raw” or “sour” natural gasses. Amine gas sweetening is a proven technology that removes H2S and CO2 from natural gas and liquid hydrocarbon streams through absorption and chemical reaction. The entire process is very energy intensive and results in a large operating cost. Optimizing the amine activity and usage by on line analysis is a critical step in reducing overall costs and measuring the efficiency of the CO2 capture at the same time.
During the blending process, different fractions of the crude oil distillation are mixed together to produce ready-to-sell diesel or gasoline. This process is the most economical when it is carried out in automated process systems that work online. The endpoint of the blending process is reached when the required fuel specifications are achieved. Key characteristics which indicate the progress of the blending process are the Cetane number for diesel blends and the octane rating for gasoline blends. Near-infrared spectroscopy (NIRS) sensors located directly in the process enable the entire process to be controlled and ensure a high-quality end product.
Approaching 150 million tons per year, ethylene is the largest volume industrially produced organic material. Feedstock, typically naphtha or light gases (e.g., ethane, propane), is first heated to high temperatures to break down the feed into small hydrocarbon molecules. After being cooled, the products are then sent through a variety of separation processes with one product stream among many being high purity ethylene.
Refining is a water intense process. Many of the processes in a petroleum refinery use water in large quantities. Refineries also generate a significant amount of wastewater that has been in contact with hydrocarbons and most organic and inorganic compounds found in the refinery accumulate in this process water. To sustain this resource, refineries treat the waste water and reuse it for various process applications. This requires treatment and reuse process requires reliable analysis that monitors the composition of the water continuously.
Refineries are complex systems of multiple operations that depend on the type of crude refined and the desired products. They constantly optimize the production process to improve the high-value products yield that maximizes profitability. Refineries lose their profit due to the corrosion to the level of $1 billion per year. Protecting refinery plants against corrosion due to the sulfur, chloride and other organic acids is important in regard to safety and profitability. Metrohm offers innovative and improved analytical methodologies to improve process efficiency and to protect against corrosion to maximize profitability.